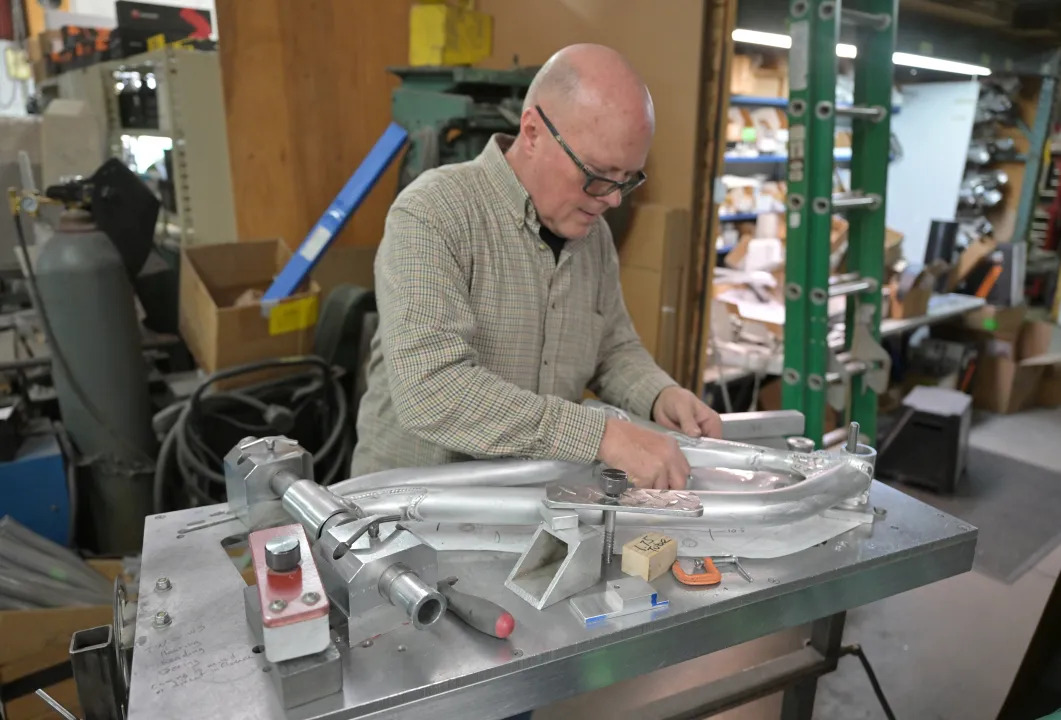
Devin Lenz puts a frame of a full-suspension mountain bike on a welding board at his workshop this week in Fort Lupton. Lenz builds high-performance mountain bikes and ski bikes. (RJ Sangosti/The Denver Post)
In a backyard workshop behind his home in rural Weld County, Devin Lenz is explaining his obsession with designing and building things, a passion dating back to his boyhood in the 1970s when he was a BMX rider. His father was a guitar maker — a luthier — who also built drag racing cars. Young Devin was captivated.
“He was building guitars, and I would go to work with him when I was a kid and goof around with the tools,” said Lenz, who grew up in Westminster. “I also worked for him, so I learned a lot about building stuff. I’ve always been fascinated by it. For some reason, I’ve got this knack for designing — looking at stuff and trying to figure it out.”
Lenz, 60, followed his passion and became a builder of full-suspension mountain bikes and ski bikes, machining parts and assembling them by himself in his workshop 6 miles north of Brighton in Fort Lupton under the brand name Lenz Sport. He is a man of many jobs — designer, machinist, toolmaker, welder, color-coating technician — a one-man assembly line. There’s just one thing he isn’t very good at.
“Not a very good marketer,” he confessed with a smile while a jazz station provided background music. “Not a very good salesperson at all.”
He sells 50 to 60 mountain bikes annually, and last year he sold about 100 ski bikes, which was his best year in that part of the business. His ski bikes cost from $2,000 to $4,000, while mountain bikes fetch $5,000 to $10,000. “All high-end, boutique-level stuff,” Lenz said.
One of his competitors is highly complimentary. Chase Wagstaff, co-founder of Sno-Go — a product that is similar to a ski bike, except Sno-Gos have three skis instead of two — said he considers Lenz to be the best competitor in the marketplace.
“He’s like an artisan,” Wagstaff said. “He makes incredible bikes.”
Lenz built his mountain bike prototype in 1996 and began selling them in 1997. A decade later, he began designing and building ski bikes. Diversifying might have saved his business.
“Being a small business, I’m always barely getting by, making mountain bikes,” Lenz said. “Then you get into the winter months, really struggling because there’s no sales of mountain bikes. When I started doing the ski bikes, it was some income during the winters. It really kind of kept me going. I don’t know if I’d still be doing it after all these years. In the winter it was always so tight with the cash flow. Now with ski bikes, I’m still not making great money, but I’m busy all the time.”
Lenz vividly recalls his first run on a ski bike he built.
“I was up at Copper Mountain at the top of the American Flyer lift,” Lenz said. “It’s pretty mellow at first, so you’re steering around and it’s kind of fun. But once it starts getting steeper, putting it on edge, you’re carving. That’s how you go fast, putting it up on edge. I was just cruising around, every run for the first year, just grinning from ear to ear. Jumping was scary, because you didn’t know what was going to happen when you landed.”
That winter of testing — somebody had to do it, after all — showed him his first design needed major improvements.
“It was long and rode like a freight train,” Lenz said. “It just wasn’t very good. I figured I needed to shorten things, making it tighter and lighter, and simplify it. I built that bike, and it was just amazing. It just rode so well. It was really good in the bumps, really quick, fast and agile.”
He buys raw aluminum in 12-foot pieces, cuts them into blanks, shapes the blanks into bike parts he designs with the help of computer-aided drafting and transforms them into components. His computer generates programs that run a milling machine, essentially whittling parts from the blanks.
“It’s super expensive to have machine parts made,” Lenz said. “I probably couldn’t do this if I wasn’t making the parts myself.”
He also can take the tubes that make up his frames and bend them into nice curves on a hydraulic press he built.
He loves to explain how he does it all and to show off his equipment, including the electrostatic powder coating machine he uses to apply vibrant colors to his aluminum frames. An electrostatic spray gun applies a positive charge to the coloring material, while the piece being sprayed is grounded electrically, helping to bind the color coating.
“You get a nice, even coat on it. You stick it in the oven and it bakes on, cross-links the molecules and binds it on there,” Lenz said. “It’s essentially a plastic coating.”
Lenz isn’t getting rich, but he has a niche, and he gets to indulge his passion for designing things. It’s on his mind day and night.
“I can’t stop,” Lenz said. “There will be times I go to bed, or I’m taking a shower, and I’m thinking about designing something — how you’re going to do this or do that. I’ve got other ideas now that I waste time thinking about making. Like, I want to make my own glasses. I like designing and building stuff, figuring out how to do it. It’s just a challenge.”
This story was originally published by The Denver Post, a BusinessDen news partner.
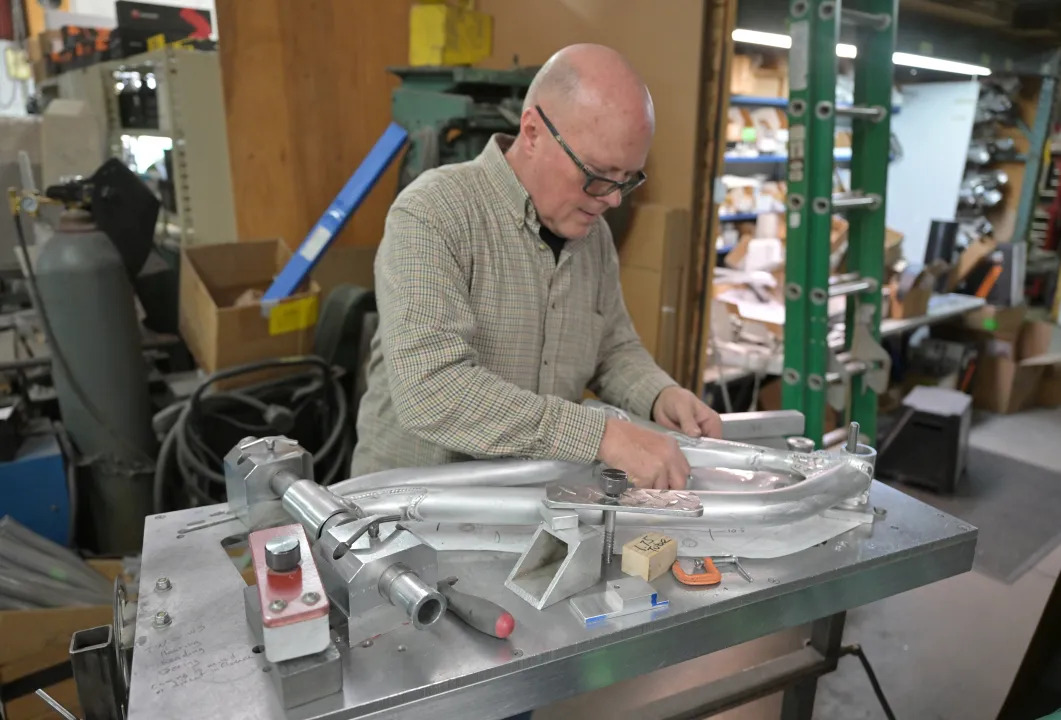
Devin Lenz puts a frame of a full-suspension mountain bike on a welding board at his workshop this week in Fort Lupton. Lenz builds high-performance mountain bikes and ski bikes. (RJ Sangosti/The Denver Post)
In a backyard workshop behind his home in rural Weld County, Devin Lenz is explaining his obsession with designing and building things, a passion dating back to his boyhood in the 1970s when he was a BMX rider. His father was a guitar maker — a luthier — who also built drag racing cars. Young Devin was captivated.
“He was building guitars, and I would go to work with him when I was a kid and goof around with the tools,” said Lenz, who grew up in Westminster. “I also worked for him, so I learned a lot about building stuff. I’ve always been fascinated by it. For some reason, I’ve got this knack for designing — looking at stuff and trying to figure it out.”
Lenz, 60, followed his passion and became a builder of full-suspension mountain bikes and ski bikes, machining parts and assembling them by himself in his workshop 6 miles north of Brighton in Fort Lupton under the brand name Lenz Sport. He is a man of many jobs — designer, machinist, toolmaker, welder, color-coating technician — a one-man assembly line. There’s just one thing he isn’t very good at.
“Not a very good marketer,” he confessed with a smile while a jazz station provided background music. “Not a very good salesperson at all.”
He sells 50 to 60 mountain bikes annually, and last year he sold about 100 ski bikes, which was his best year in that part of the business. His ski bikes cost from $2,000 to $4,000, while mountain bikes fetch $5,000 to $10,000. “All high-end, boutique-level stuff,” Lenz said.
One of his competitors is highly complimentary. Chase Wagstaff, co-founder of Sno-Go — a product that is similar to a ski bike, except Sno-Gos have three skis instead of two — said he considers Lenz to be the best competitor in the marketplace.
“He’s like an artisan,” Wagstaff said. “He makes incredible bikes.”
Lenz built his mountain bike prototype in 1996 and began selling them in 1997. A decade later, he began designing and building ski bikes. Diversifying might have saved his business.
“Being a small business, I’m always barely getting by, making mountain bikes,” Lenz said. “Then you get into the winter months, really struggling because there’s no sales of mountain bikes. When I started doing the ski bikes, it was some income during the winters. It really kind of kept me going. I don’t know if I’d still be doing it after all these years. In the winter it was always so tight with the cash flow. Now with ski bikes, I’m still not making great money, but I’m busy all the time.”
Lenz vividly recalls his first run on a ski bike he built.
“I was up at Copper Mountain at the top of the American Flyer lift,” Lenz said. “It’s pretty mellow at first, so you’re steering around and it’s kind of fun. But once it starts getting steeper, putting it on edge, you’re carving. That’s how you go fast, putting it up on edge. I was just cruising around, every run for the first year, just grinning from ear to ear. Jumping was scary, because you didn’t know what was going to happen when you landed.”
That winter of testing — somebody had to do it, after all — showed him his first design needed major improvements.
“It was long and rode like a freight train,” Lenz said. “It just wasn’t very good. I figured I needed to shorten things, making it tighter and lighter, and simplify it. I built that bike, and it was just amazing. It just rode so well. It was really good in the bumps, really quick, fast and agile.”
He buys raw aluminum in 12-foot pieces, cuts them into blanks, shapes the blanks into bike parts he designs with the help of computer-aided drafting and transforms them into components. His computer generates programs that run a milling machine, essentially whittling parts from the blanks.
“It’s super expensive to have machine parts made,” Lenz said. “I probably couldn’t do this if I wasn’t making the parts myself.”
He also can take the tubes that make up his frames and bend them into nice curves on a hydraulic press he built.
He loves to explain how he does it all and to show off his equipment, including the electrostatic powder coating machine he uses to apply vibrant colors to his aluminum frames. An electrostatic spray gun applies a positive charge to the coloring material, while the piece being sprayed is grounded electrically, helping to bind the color coating.
“You get a nice, even coat on it. You stick it in the oven and it bakes on, cross-links the molecules and binds it on there,” Lenz said. “It’s essentially a plastic coating.”
Lenz isn’t getting rich, but he has a niche, and he gets to indulge his passion for designing things. It’s on his mind day and night.
“I can’t stop,” Lenz said. “There will be times I go to bed, or I’m taking a shower, and I’m thinking about designing something — how you’re going to do this or do that. I’ve got other ideas now that I waste time thinking about making. Like, I want to make my own glasses. I like designing and building stuff, figuring out how to do it. It’s just a challenge.”
This story was originally published by The Denver Post, a BusinessDen news partner.